Predictive Maintenance vs Preventive Maintenance : Key Differences Outlined
2024-07-17
The industries these days rely on heavy machinery which cannot be purchased frequently. They depend on the reliability and efficiency of the equipment. Businesses ever since have been having the debate over predictive maintenance vs preventive maintenance for choosing the best. This helps them to reduce downtime and increase productivity. In a nutshell, predictive maintenance software relies on data and past trends to schedule any maintenance tasks while preventive maintenance software works on scheduled maintenance to prevent issues. However, a brief idea is not enough to understand the depth of these concepts. Hence, we’ll be looking at the details in the blog. Understanding the key differences in these concepts will help the businesses determine what suits them best.
“Maintenance is one of those areas where you can either pay now or pay later, but if you wait until later, it always costs more.”- Dave Turbide
Understanding Predictive Maintenance
Predictive maintenance is a proactive approach. It uses data analytics and monitoring to gauge any possible failure that might occur. This strategy relies on sensors and other advanced analytics to collect real-time information. These data might include things like vibration, temperature and pressure levels. We analyze this data to predict any patterns that might cause future failures.
By forecasting the issues before they occur, predictive maintenance allows targeted maintenance. It minimizes the downtime and reduces maintenance charges. According to a report by McKinsey & Company, predictive maintenance can reduce machine downtime by 30-50% and extend the lifespan of aging assets by 20-40%. Hence, predictive maintenance makes the equipment more efficient and reliable by embracing a proactive approach.
Understanding Preventive Maintenance
Preventive maintenance is a plan maintenance strategy that prevents unexpected equipment failures. It involves regular PM schedules and servicing of the equipment. This approach works on time or usage intervals regardless of the current condition of the machine. The plan of preventive maintenance is to catch the issue early on and avoid any major downtime from happening.
The planned maintenance system involves cleaning, lubricating, adjusting and replacing the maintenance tools and equipment. We consider all of these as downtime reduction strategies. For instance, the healthcare industry performs time based maintenance of MRI machines so that they function properly. The simplicity and predictability of preventive maintenance makes it a widely accepted practice for condition-based maintenance as well. According to a study by Plant Engineering, 78% of companies use preventive maintenance as a key part of their maintenance programs.
The preventive maintenance tool at AntMyERP will help you with asset management optimization like no other as it is cost effective and has some top notch features. Book a demo with us today to know more about what we have to offer.
Predictive Maintenance vs Preventive Maintenance
We know it can be quite difficult to choose the best maintenance practice. Hence, we’ll be discussing the key differences between the two to make your job easier.
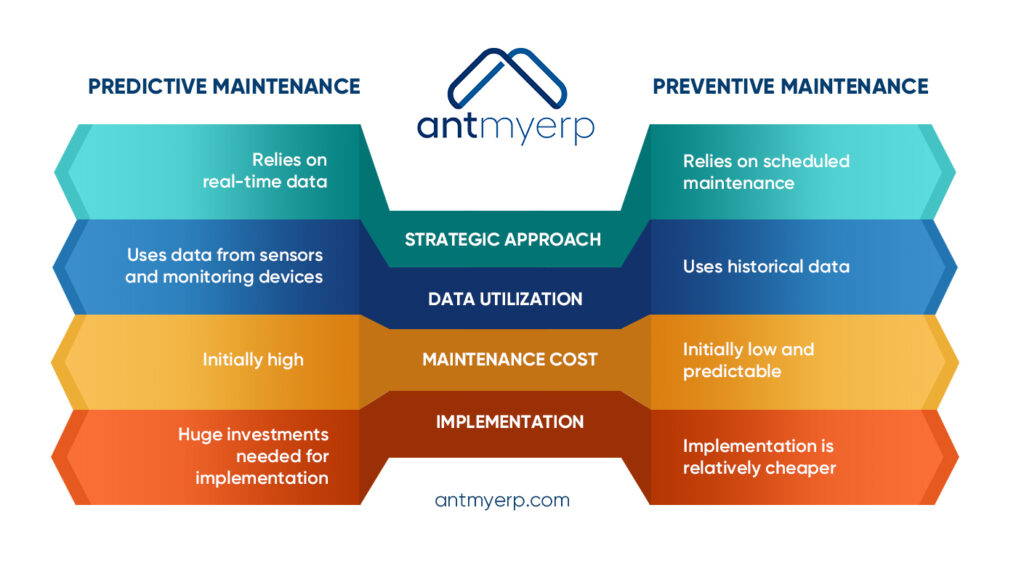
Strategic Approach
Preventive maintenance follows scheduled maintenance strategies, performing tasks at regular intervals. This doesn’t consider the condition of the equipment. However, predictive equipment maintenance relies on real time data and analytics. Predictive analytics maintenance target on the actual condition of the equipment.
Data Utilization
Preventive maintenance uses data from the manufacturer or historical data to schedule maintenance tasks. However, predictive maintenance uses sensors and monitoring devices to gauge the condition of the equipment and work on targeted parts.
Maintenance Cost
We should highly consider optimizing maintenance costs. The cost of preventive maintenance is regular and predictable. However, the cost might increase in the long run due to over-maintenance. Meanwhile, preventive maintenance optimization can be costly due to the need for sensors, data analytics tools and skilled staff. But, in the long run it can significantly help in cost savings as it works on targeted areas and increases the lifespan of the machine.
Implementation
In terms of implementation complexity we can say that preventive maintenance is relatively easier to implement. It requires less advanced technology and requires basic management. However, predictive maintenance requires huge investment but offers long term benefits as well.
Choosing the Right Maintenance Strategy for Your Business
Selecting the apt maintenance strategy involves predictive maintenance vs preventive maintenance evaluation in terms of industry type, implementation strategy, budget and operational complexity. The goal of debating over predictive maintenance vs preventive maintenance should end on reaching what the company needs. This should include reducing the downtime through real time data analysis. While both the approaches work in their own effective ways, find what your business needs.
Catch up with the team at AntMyERP today for free consultation and decide!
Cite predictive maintenance vs preventive maintenance examples.
Predictive Maintenance Example
Manufacturing Industry: In a manufacturing plant, vibration sensors are installed on critical machinery. These sensors continuously monitor the vibration levels and send data to a predictive maintenance system. The system analyzes the data to identify patterns indicating potential bearing failures. Maintenance is scheduled just before the bearing is expected to fail, preventing unplanned downtime and reducing repair costs.
Preventive Maintenance Example
Healthcare Industry: In a hospital, regular monthly inspections and servicing of MRI machines are scheduled. Technicians perform routine tasks such as cleaning, calibrating, and replacing parts based on the manufacturer’s recommendations. This ensures the equipment remains operational and reduces the likelihood of unexpected breakdowns, maintaining high reliability and safety standards for patients.
Next Steps
Book a 15 day free trial with us!
Get the detailed field service software pricing here.
Want to get ensured before you invest? We got you covered! Find the reviews of some of our clients here.