AntMyERP's Preventive Maintenance Checklist
Boost Performance with Preventive Maintenance Checklist
Welcome to our Preventive Maintenance Checklist! This is the place to be if you want to make sure your equipment and assets stay in excellent condition and perform at their best for a long time. Keeping up with regular maintenance is really important. It helps you avoid costly breakdowns and makes sure your operations run smoothly and efficiently. Our equipment maintenance checklist is here to help you take care of your devices, systems, and services.
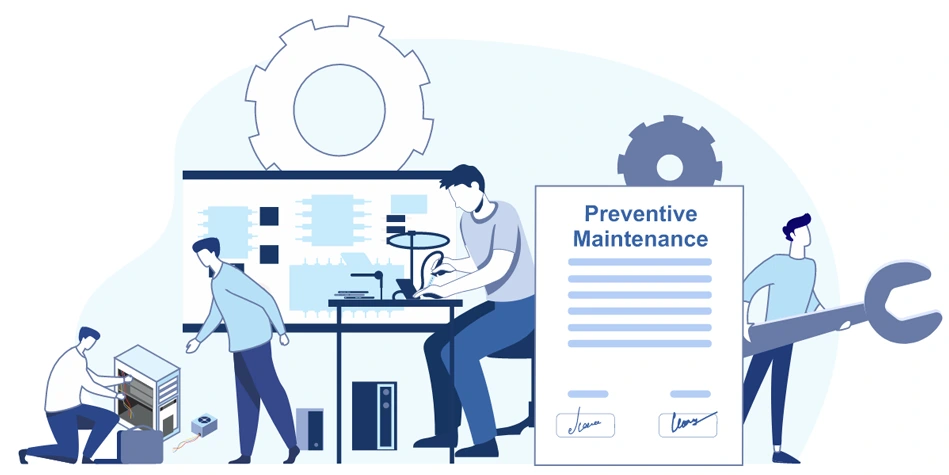
Key Elements of Our Maintenance PM Checklist
Every company should prepare a checklist before performing preventive maintenance on any machine or piece of equipment.
Make a checklist for preventive maintenance in the “to do” section. Our templates are all configured for you, so you can easily fill in all the details using the parameters. Â
Connect the PM maintenance checklist to the problem at hand. So, whenever you log a call about any problem, this checklist will appear for you. You can even create your very own checklist in the masters. It’s designed to make your business process easier by allowing you to create as many equipment maintenance checklists as you need.
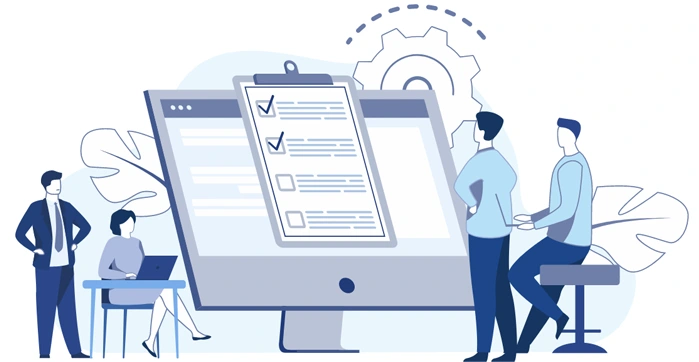
Type of Preventive Maintenance Checklist
Take a look at our collection of features tailored to industry-specific checklists.

All Services Checklist
Sometimes, when a technician comes to check on a device and it’s already working fine, they just leave without doing anything. They still write a report and ask the customer to sign it to confirm that everything is okay. This can lead to a big problem for the device down the line, which could result in a significant loss for the company. Using our ‘All Services Checklist’, keep an eye on its progress, figure out how urgent it is, and assign technicians to work on it step by step from the checklist.Â

Spare Parts & PM Maintenance Checklist
Use the Machine Maintenance Checklist to keep track of all the project management requests made by various vendors and clients simultaneously. In a single digital setting, you can learn essential details like the requester firm name, service ticket number, due date, latest activity, pending days, and contract type. Use the Spare Parts Checklist to see how many parts were requested, fixed, replaced, or refused for each piece of machinery or equipment during the preventative maintenance service.

Defective & Pending Returns Checklist
You can use the Defective Returns Checklist to find out if the faulty items are still with the field engineers or if they have been brought back to the company’s inventory. Find and get reports of the maintenance services that were done to a company’s machines and equipment. You can download these reports using the unique serial number of each machine.
features