Causes of Equipment Failure and Preventive Maintenance Strategies
2024-08-23
The industrial world today is humongous and relies on the effective use of equipment for smooth operations. This plays a major role in the success of the business. Whether it is energy, construction, manufacturing or any other sector, equipment plays a vital role. However, equipment failure can lead to major consequences like costly equipment downtime, financial losses and even safety risks. To mitigate these incidents it is essential for the industries to follow the preventive maintenance strategies so that major losses are minimized.
Understanding the causes around equipment failure is essential for equipment based industries. The failure is not just an inconvenience but a significant disruption to the entire workflow. These causes can range from minor wear and tear to complex installation issues. Preventive maintenance is designed to work on such causes of failure. Equipment maintenance involves regular inspections, timely repairs and other maintenance management techniques.Â
In this blog, we will explore common causes of equipment failure. We will also look into preventive maintenance strategies to mitigate those causes. By understanding and addressing the key areas, organizations can enhance their operational efficiency and productivity. Here, AntMyERP can be your one stop solution for all the preventive maintenance strategies. Let’s delve into it.
Causes of Equipment Failure
Equipment failure can rise from various factors. Understanding them is the first step for failure prevention. Let us take a look at some of the common causes:
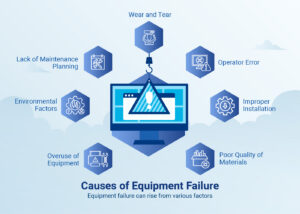
Wear and TearÂ
Wear and tear of equipment can happen over time. When you use equipment exhaustively without monitoring its health, wear and tear become inevitable. However, you can manage this by regularly scheduling maintenance and replacing parts on time. On the other hand, continuous friction within the between parts and exposure to open environments can lead to further wear and tear. In such cases lubrication and protective coating can help curb the issue.
Lack of Maintenance Planning
Failing to perform regular condition based maintenance can result in major problems. Some companies neglect regular inspection and root cause analysis at an early stage to save cost. Such issues can become a major downtime, high repair costs and major downtime in the long run.Â
Operator Error
Insufficient training of the employees who are liable to perform the operations can cause severe damage. This can come in forms of improper handling, incorrect usage and failing to follow the operational procedures. This can stress equipment beyond limit and can result in premature failures. Sometimes, even trained personnels ignore minor issues and take them for granted which can lead to major failures later.
Environmental Factors
Exposure to extreme temperatures whether hot or cold can lead to poor performance of the equipment. Similarly humidity and dust can also affect the equipment in adverse ways. In such cases preventive maintenance techniques can play a major role in curbing the issues.Â
Improper Installation
Installation comes with a set of manufacturer’s guidelines. Failing to install the equipment according to the guidelines can result in a range of problems like misaligned components, loose ends etc. Also, failing to calibrate the equipment during installation can lead to incorrect readings and disrupted operations in the long run.Â
Overuse of Equipment
Equipment function best when operated under certain conditions and in their capacity. Overusing or overloading the equipment can cause severe damage to them. Continuous operations without regular and predictive maintenance can cause the equipment to die down sooner.
Poor Quality of Materials
Companies go way and beyond to save their costs in all possible ways. However, this might result in fatal consequences. Using poor quality material to save cost can lead to premature wear and tear and sometimes safety concerns too. Incompatible materials can lead to rapid degradation and failure of components.
Impact of Equipment Failure
Equipment failure can have significant and widespread negative consequences. One of the most obvious and immediate consequences is the downtime. When a part of the equipment stops functioning, it leads to a halt in the production line. This unplanned downtime can lead to huge revenue losses and missed deadlines.Â
Additionally, equipment failure can result in increased repair cost. When an organization misses reliability-centered maintenance and a major breakdown occurs, it pays a huge sum to fix it. Another, critical impact is the safety hazards to the employees as a result of equipment failure. If you overlook or fail to follow preventive maintenance strategies, the hazards can become fatal. This eventually damages the company’s reputation.Â
Preventive Maintenance Strategies
After discussing the causes of equipment failure, let us look at the preventive maintenance strategies to mitigate those.
Scheduled Maintenance
Scheduled maintenance involves regular inspections and servicing regardless of the condition of the equipment. This approach helps to inspect the potential issues early on before it becomes a massive problem. Timely replacement of spare parts of the equipment helps to increase its lifespan and enhances operational efficiency.
Predictive Maintenance
Predictive maintenance uses algorithms and data analytics to predict signs of equipment failure. By identifying signs from sensors and detectors, the issues are caught early on. Predictive maintenance is condition-based maintenance unlike preventive maintenance. This means that predictive maintenance is carried out only after an issue has been detected. It does not have to happen in regular intervals.
Operator Training
Properly trained employees and field service personnel are essential to prevent the losses. Training programs should focus on enhancing their skills in handling the equipment appropriately. Well trained operators can take up basic maintenance tasks such as cleaning, lubricating and checking for leaks. Additionally, operators should be trained to report issues or anything that they find out of order early on.
Use of High Quality Parts
Investing initially on high quality parts can be beneficial in the long run. Inferior spare parts can make the equipment susceptible to major failures at early stages. Choosing the right parts for the equipment can increase the lifespan of the equipment. The organizations should build a healthy relationship with the vendors who can supply genuine and high quality parts.
Proper Documentation
Properly documenting the details related to preventive maintenance helps in multiple ways. Firstly, the detailed documentation including information about the inspections, repairs, part replacements etc. can help detect the recurring problems and hence address them efficiently. Furthermore, in industries where compliance is critical, the documentation ensures adherence to maintenance standards. This helps the organization to reduce risk of penalties thus enhancing organization’s credibility.
Conclusion
Preventive maintenance strategies are essential for minimizing equipment failures, reducing downtime and enhancing operational efficiency. By understanding the causes and impact of the equipment failure, one can easily understand the need for implementing preventive maintenance strategies. By adopting the best practices, one can easily ensure the benefits in the long run. The proactive measures not only increase the lifespan of the equipment but also contribute to the safe and productive environment to work on.Â
Comment down the questions you have related to the implementation of preventive maintenance strategies and we will be more than happy to help.
Next Steps
Book a 15 day free trial with us!
Get the detailed field service software pricing here.
Want to get ensured before you invest? We got you covered! Find the reviews of some of our clients here.