Streamline Operations with Spare Parts Management Software
When it comes to inventory management, most people think about the big items—those that arrive, get used, and move out. But for businesses in the service industry, the challenge goes beyond that. It’s about the small but crucial spare parts, the ones that either get sent for repair, replaced, or discarded after use. Keeping track of these minor components is where most businesses struggle. This is where AntMyERP’s Spare Parts Management Software becomes a game-changer, offering a seamless way to manage, track, and optimize every part of the inventory.
In a service-driven business, even the tiniest spare part can hold immense value. Losing track of these components leads to inefficiencies, inventory leakages, and financial losses. That’s why having a spare parts management system is not just beneficial—it’s essential.
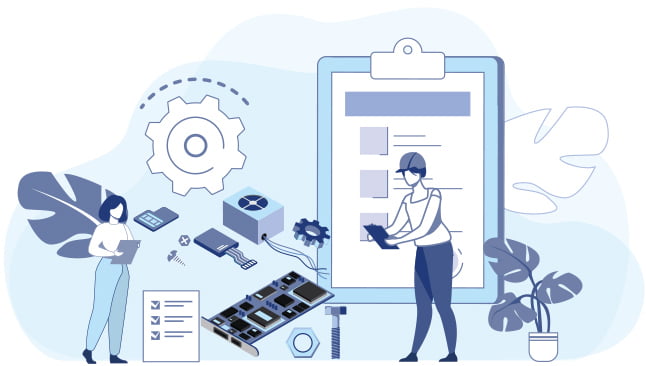
Spare Purchase with Parts Inventory System
Managing spare parts procurement shouldn’t feel like a guessing game. With AntMyERP’s spare parts inventory software, businesses can purchase, track, and monitor their spares efficiently. Engineers working on-site can raise purchase requests, ensuring that necessary parts are available when needed. Instead of manually tracking what’s in stock and what’s running low, the system provides real-time updates, preventing both overstocking and shortages. Each part’s movement—whether incoming, outgoing, or in storage—is meticulously logged, eliminating any uncertainty in inventory management. With instant notifications, the management team stays informed about every part used for repairs and every request raised for service closures.
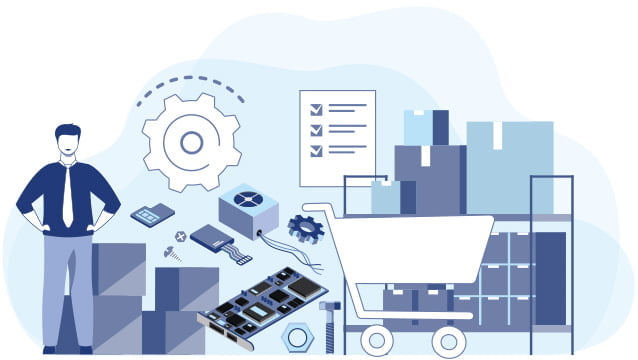
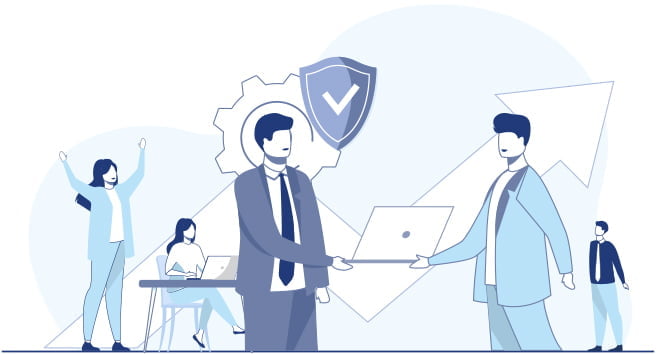
Asset Issue with Spares Inventory Management Software
Misplaced spare parts often go unnoticed until they cause major setbacks. The inability to track smaller inventory items leads to revenue leaks that are difficult to quantify but substantial in impact. AntMyERP puts a stop to these leakages.With a well-structured system, businesses can maintain a record of every spare part issued to employees, whether for preventive maintenance or incident management. If a part is provided for a repair and isn’t used, the system keeps the service ticket open, ensuring it is either returned or reassigned. The software’s ease of tracking allows management to have complete visibility over every issued asset, ultimately saving engineers’ time and boosting operational efficiency.
Insights on Spares Management Software
Keeping track of spare parts is one thing; making informed decisions based on real-time data is another. AntMyERP’s reporting system delivers precise insights into every aspect of spare parts management. From monitoring spares requested by engineers to tracking defective parts pending return, businesses get an end-to-end view of their inventory movements. The system also maintains a spare scrap register, ensuring that every discarded part is documented and accounted for.

Spare Request by Engineers
For engineers on the field, spare part requests should be a seamless process. Through the Technician Mobile App, they can quickly raise a request for any required part. The coordinator can approve or reject the request based on priority and availability, ensuring smooth workflow management. The system also provides clarity on pending service tickets that require spare parts, ensuring they are resolved efficiently.

Pending Defective Spare
Managing defective spare parts is a common challenge, especially for companies handling multiple client service calls and a vast workforce of engineers. AntMyERP offers a streamlined way to track defective parts pending return, ensuring that nothing is lost in the shuffle. If a defective part can be repaired, it is sent for servicing; if it is beyond repair, it is removed from the inventory to avoid unnecessary stockpile.

Scrap Spare Register
A spare part that can no longer serve its purpose needs to be properly accounted for before being scrapped. With AntMyERP’s spare parts management software, every discarded part is logged into the system after a thorough quality check. The record helps businesses maintain transparency in inventory and prevent unnecessary losses. Field service management is incomplete without a robust spare tracking system, and this register ensures full control over what stays and what goes.
Loan/ Repair Spare Parts with Parts Management Software
Tracking spare parts sent for repair is often overlooked, leading to confusion and losses. With AntMyERP’s intelligent tracking, businesses gain full control over every spare part’s journey. If a component is out for repair, its status, location, and estimated return date are updated in real-time. This eliminates delays and ensures timely retrieval of repaired parts, preventing unnecessary reorders.
With full visibility into spare parts inventory, businesses can ensure swift responses to customer requests, optimize resource allocation, and reduce manual effort. AntMyERP simplifies every aspect of hardware spare parts management, freeing up valuable time for service teams to focus on what truly matters—delivering exceptional service.
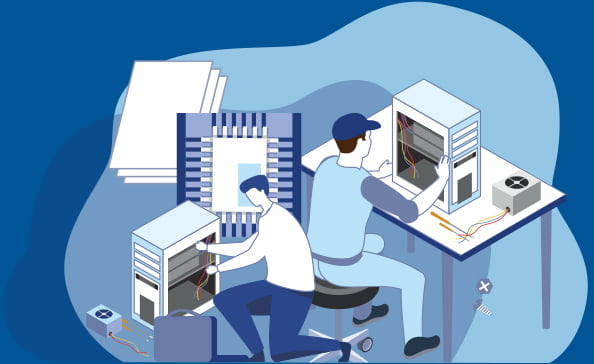
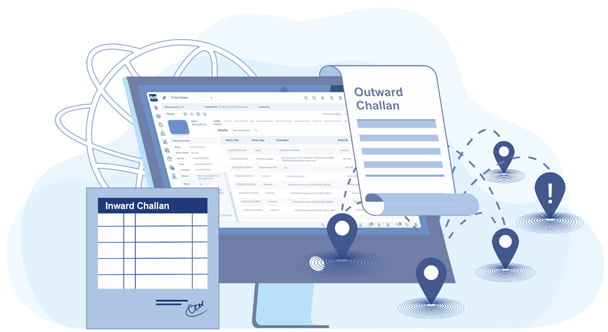
AntMyERP’s Unique Parts Management System
Register a freshly-acquired spare part by inserting its serial number through the software’s digital dashboard. Allow technicians to request a new spare part via the app with a few taps to use it for any pending field service.
Track all pending requests for issuing spare parts for use in any device. Get insights into the delay time, the current status of the request and the action required by the spare parts coordinator on the spot via spare parts management software.
Know all the approved spare parts requests on the portal based on the company name, date and ticket number. Find the quantity of approved spare parts for a product and access its challan number and date without further ado.
View the list of all rejected spare parts requests through our spare parts management software. Mention the reason for rejection, update the real-time status and find details of the manager who rejected the request quickly.
Maintain an online register of all the defective spare parts returned to your enterprise either by the customer or vendor. Decide which defective spare part to send for repair and which to eliminate from the possession, hence, saving costs.
Enhanced Spare Parts Management with AntMyERP
In today’s fast-paced business environment, relying on manual processes for inventory tracking is a recipe for inefficiency. The world runs on automation, precision, and real-time data. Spare parts, though small, come with a hefty price tag, and no business can afford to misplace or mismanage them. AntMyERP ensures complete control over spare inventory, allowing businesses to minimize losses, improve service response times, and make data-driven decisions.
Real-time Insights
You can get instant updates on individual services or service groups. You can also download auto-generated spare parts consumption reports for a customer or vendor. With this, you can analyze the reports and make informed decisions depending on the profitability.
Spare Parts Assignment
You can assign the spare parts to the service technician or service groups depending on the need. If the need not be, you can cancel the request. The assignment also depends on the availability of the spare parts.
Spare Parts Approval
You can approve or reject the spare parts request made by the technician through spare parts management software. You can notify them about the availability of a spare part and ask them to reschedule the service accordingly.
Elevate your Business with Spare Parts Management Software
FAQs
The purpose of spare parts management is to ensure the right parts are available at the right time to minimize equipment downtime, reduce operational disruptions, and optimize inventory costs. It helps maintain smooth operations and improves overall equipment reliability and efficiency.
The main problem of spare parts management is striking a balance between overstocking and stockouts. Overstocking ties up capital and increases storage costs, while stockouts can lead to equipment downtime, delayed repairs, and customer dissatisfaction, impacting overall business efficiency.
KPIs (Key Performance Indicators) in spare parts management measure the efficiency and effectiveness of inventory processes. Common KPIs include fill rate (availability of parts), inventory turnover (frequency of stock usage), stock accuracy, and lead time. These metrics help optimize inventory levels and improve service reliability.
Controlling spare parts inventory involves forecasting demand, categorizing parts based on usage and criticality, and setting optimal reorder levels. Regular inventory audits, accurate data tracking, and leveraging inventory management software also help ensure availability while minimizing excess stock and storage costs.
To reduce spare parts consumption, focus on preventive maintenance to minimize wear and tear, train staff on proper equipment handling, and ensure high-quality parts are used to extend their lifespan. Monitoring usage patterns and addressing root causes of frequent failures can also significantly lower consumption.
Spare parts management software benefits industries with complex equipment and maintenance needs, such as manufacturing, automotive, aviation, energy, construction, healthcare, and logistics. These industries rely on efficient spare parts tracking to minimize downtime, optimize inventory, and improve operational efficiency.
Yes, spare parts management software can track real-time inventory. It provides up-to-date information on stock levels, usage rates, and parts location, allowing businesses to make informed decisions on reordering and restocking. This real-time visibility helps prevent stockouts, reduce excess inventory, and ensure smooth operations.
Yes, spare parts management software can integrate with other systems like ERP (Enterprise Resource Planning) or CMMS (Computerized Maintenance Management Systems). This integration ensures seamless data flow between systems, enabling better inventory tracking, maintenance scheduling, procurement, and overall operational efficiency across the business.
Yes, spare parts management software typically supports multi-location inventory management. It allows businesses to track inventory across different warehouses, service centers, or production facilities. This feature ensures real-time visibility of stock levels at various locations, improving parts availability and optimizing resource distribution.
Spare parts management software assists in vendor and supplier management by tracking supplier performance, managing purchase orders, and maintaining accurate records of lead times, costs, and delivery schedules. It helps businesses evaluate and select reliable suppliers, streamline procurement processes, and ensure timely availability of parts, reducing delays and optimizing costs.
Yes, spare parts management software can be customized to meet specific business needs. It offers flexible configurations, such as tailored workflows, inventory categorization, reporting features, and integration with other systems. This customization ensures the software aligns with unique operational requirements, improving efficiency and addressing industry-specific challenges.
Yes, spare parts management software typically provides analytics and reporting tools. These features allow businesses to analyze inventory trends, track key metrics like turnover rates, stockouts, and lead times, and generate detailed reports on parts usage and procurement. This data helps in making informed decisions, optimizing inventory, and improving overall efficiency.
features